Description
6000/CPH Canning Line For Carbonated Soft Drinks:
No | Name | Model | Capacity | Qty. | Remark |
Item 1 – Beverage mixing system, 2 ton/hour | |||||
1 | High-shear emulsifying tank | ET-500L | 500L | 1 set |
※Material: SUS304 ※Insulated type, three layers ※Steam type ※Including Sampling port |
2 | Hygienic pump | YA3T/24 | 3000L | 1 set |
※Material:SUS304 Lift:24m Power:1.5kw |
3 | Double filter | SL300 | 3000L | 1 set |
※Material:SUS304 Filter:100mesh |
4 | CIP back pump | YA10T/24 | 10000L | 1 set |
※Capacity:12000liter/h Lift:24m |
5 | Blending tanks | HZ2500L | 2000L | 3 set |
※Material:SUS304, 2mm ※Jacketed layers ※Power:2.2kw ※Including Sampling port |
6 | Operator platform | 1 set | ※SUS304 | ||
6 | Hygienic pump | YA3T/24 | 3000L/H | 1 set |
※Material:SUS304 Lift:24m Power:2.2kw |
7 | Double filter | SL300 | 3000L | 1 set |
※Material:SUS304 200mesh |
8 | Carbonator | IN-QHS-2000 | 2T/H | 1 set |
※Siemens PLC+HMI ※Mixing ratio:3.8-4.2 (Same with Coca colo), with proportional valve ※CO2 filtering and pressure regulating system ※CO2 pressure balancing system ※With vacuuming system |
9 | CO2 Filter | CO-2 | 4T/H | 1 set | |
10 | CIP system | CIP-3*500L | 500L | 1 set |
※Steam heating ※500L lye tank ※500L acid water tank ※500L hot water tank |
11 | Plate Heat exchanger | PHE5 | 5m2 | 1 set |
※5m2 ※SUS316 contact part ※Capacity:10000liter/h Lift:24m ※Two layers, insulated type ※The system is for making cold water on 2-5Degc for mixing the beverage, |
Hygienic pump | YA10T/24 | 10000L | 1 set | ||
Cold water tank | LSG | 1500L | 1 set | ||
12 | Cooling system | IN-50S | 50HP | 1 set |
※Water cooling type ※Including cooling tower ※Pumps and pipes ※USA copeland compressor |
13 | Steam generator | IN-GL | 500Kg/H | 1 set |
※Italian Baltur burner ※Diesel type |
14 | Pipe work |
※Out surface and inner surface work handling ※On-site engineering welding ※Designed as shown in the drawing ※CIP system pipe works ※All Valves has to be butterfly valves, Flanged gasket fittings, included in chilled water, CIP station to Machines, treatment to syrup prep to carbonator to Filling Seaming. This has to include the CIP and Return Line as well. ※Drainage system pipe works ※Cooling tower pipe works ※Chilling machine pipe works ※CO2 filter pipe works ※Drainage pipe works from each machine which consumes water to the Client’s drainage point ※SUS304 drainage works |
|||
Thermal insulation |
※Cooling tower pipe thermal insulation ※Chilling machine pipe thermal insulation ※Steam pipe thermal insulation is not included |
||||
15 | Cooling tower | IN-LQT | 30ton | 1 set | ※For cooling down the sugar from high shear tank |
Hygienic pump | YA3T/24 | 3000L/H | 1 set | ※For pumping the material from the mixing tank to the PHE | |
Plate heat exchanger | PHE10 | 10m2 | 1 set | ※For cooling the material from the mixing tank | |
Item 2 – Filling & Packing Part | |||||
1 | Automatic depalletizer | IN-XD-6000 | 6000CPH | 1 set | ※SUS304 as the structure |
Inline washer | 6000CPH | 1 set |
※Can inverter ※Pumps and pipe works |
||
2 | Aluminum can filling sealing Duo-block | IN-GD18-6 | 6000CPH | 1 set |
※Siemens PLC+HMI (on the control cabinet) ※Siemens VFD speed regulation ※Autonics Sensors ※SKF bearing ※IGUS sliding sleeve ※Schneider electric components ※SUS304, 3mm supplied by POSCO, S.Korea ※24 Isobaric filling heads ※6 capping heads |
2.1 | Nitrogen dosser | DJ | 6000CPH | 1 set | |
3 | Bottle exterior rinsing | IN-XGJ | 6000CPH | 2 set |
※To wash away the beverage on the cans ※Adjustable nozzles ※Pipe works and pumps |
4 | Bottle warming machine | IN-WPJ | 6000CPH | 1 set |
※6000*1000mm ※Siemens PLC+HMI ※Siemens low voltage electric components ※Four temperature regulation zone ※Steam control system |
5 |
Can pressure tester |
NYJ-200 | 6000CPH | 1set |
※Nitrogen type ※Siemens PLC ※Real-time tracking sensor |
6 | Liquid level inspector | ZJZ-200 | 6000CPH | 1set |
※Real-time tracking sensor ※Non-contact monitoring |
7 | Blowing dryer | CGJ | 6000CPH | 1 set |
※with two 7.5 kW power fans ※Dust proof |
8 | Ink printer | VJ1210 | 6000CPH | 1 set |
※Supplied by American videojet com[any ※You can by ink in your country |
9 | Can Inverter | 6000CPH | 1 set | ||
10 | Automatic PE film shrink wrapping machine | IN-MB-150A | 6000CPH | 1 set |
※Siemens PLC+HMI ※Schneider VFD speed regulation ※Airtac Pneumatic ※Schneider electric components |
10.1 | Tray applying system | 4m | ※Applying the tray before shrinking packing | ||
11 | Flat conveyor with motors | SC-1 | 6000CPH | 50m |
※SUS304, POSCO, Korea ※Per the finalized layout ※Water collecting tray ※SUS304 cable cage ※Speed adjusting motor |
Conveying motors | 6sets | ||||
90 degree turn | 2sets | ||||
12 | Low pressure air compressing system | DY-2 | 1.8 m3/min | 1 set |
※Oil free type ※10 Bar ※Including air filter and dryer |
Beverage mixing system
1) Syrup Melting Tank
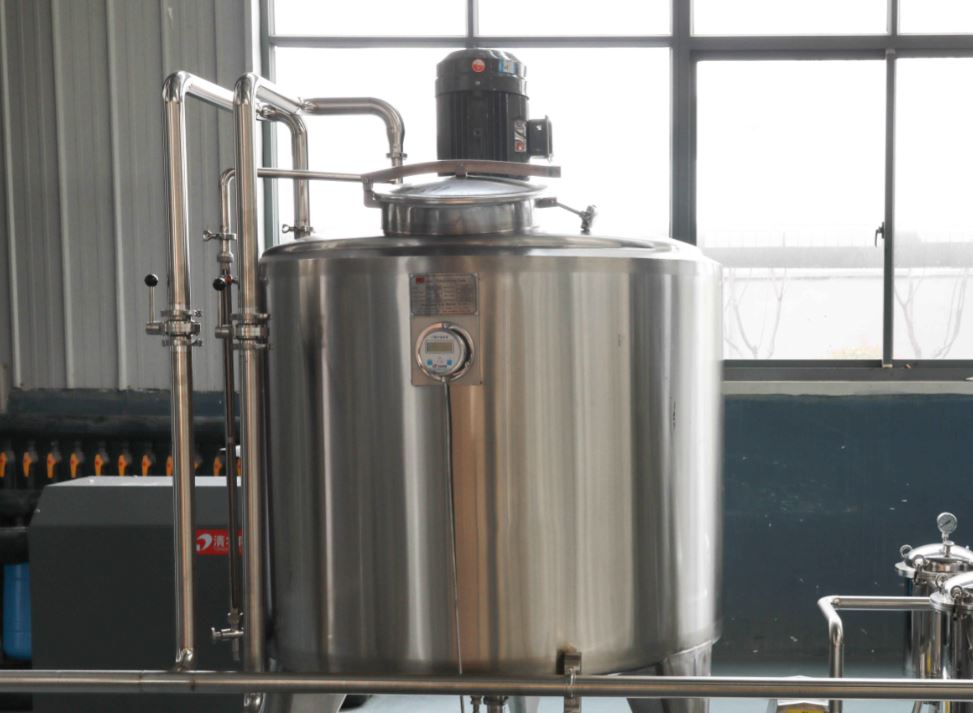
Technical parameters:
Model: |
HTG-3 |
Capacity: |
1000L |
Material: |
SUS 304 |
Dimension: |
Dia1000* Height1000 mm |
2) Double Filter
Technical parameters:
Model: |
ZPR-H2 |
Capacity: |
4000L/H |
Material: |
SUS 304 |
Working pressure: |
≤0.5Mpa |
Permanganate ratio: |
1.5/1000 |
Liquid flowing quantity: |
10L/min |
Volume of Tank: |
120L |
Permanganate’s amount: |
25 Kg |
Weight: |
129 Kg |
Static matter: |
2.8 Kg |
Absorbed matter: |
12 Kg |
3) Syrup Filter
Technical parameters:
Model: |
TJF |
Capacity: |
4000L/H |
Working pressure: |
≤0.5Mpa |
Working pressure: |
≤0.5Mpa |
Permanganate ratio: |
1.5/1000 |
Liquid flowing quantity: |
10L/min |
Volume of Tank: |
120L |
Permanganate’s amount: |
25Kg |
Net weight: |
120Kg |
Static matter: |
2.8Kg |
Absorbed matter: |
12Kg |
4) Mixing tanks
Technical parameters:
Model: |
HZ2000L |
Capacity: |
2500L |
Insulate type: |
Yes |
Agitator: |
43R/M |
Material: |
Stainless steel 304 |
Inside wall thickness: |
3 mm |
outside wall thickness: |
1.5 mm |
Tank body size: |
Φ1800*1850mm |
Overall size: |
1850*3200mm |
Total power: |
2.2kw |
Main components: |
dia400 manhole, liquid elve, CIP Cleaning ball, aseptic breath, temperature gauge, mixing motor |
5) Water chiller
Technical parameters:
Model |
IN-50S |
||
Refrigerating capacity |
153KW |
||
132359KCal/hr |
|||
Power supply |
3 phase 380V±10%:50Hz±2% |
||
Compressor |
Input power |
36.8 Kw |
|
type |
Totally closed scroll compressor |
||
Quantity |
Set |
4 |
|
Cooling water |
Input temperature |
℃ |
30 |
Output temperature |
℃ |
35 |
|
Flow |
m3/h |
27 |
|
Connector spc |
mm |
DN80 |
|
Chilled water |
Input temperature |
℃ |
2 |
Output temperature |
℃ |
-3 |
|
Flow |
m3/h |
15 |
|
Connector spc |
mm |
DN50 |
|
Chilled water pump |
Model |
Vertical type pipe water pump |
|
Power |
Kw |
5.5 |
|
Head |
M |
31 |
|
Overall size |
Length |
mm |
2400 |
Width |
mm |
1000 |
|
Height |
mm |
1800 |
|
Weight |
kg |
950 |
Main components:
No. |
Name |
Brand |
1 |
Compressor |
Copeland (USA) |
2 |
Condenser |
Imported efficient heat exchanger radiator fan with expanded connection of copper pipe& aluminium foil |
3 |
Evaporimeter |
Stainless steel efficient shell and tube heat exchanger |
4 |
Expansion valve |
Alco (USA) |
5 |
Filter |
Alco (USA) |
6 |
Solenoid valve |
Alco (USA) |
7 |
Pump |
Nanfang (top supplier in China) |
8 |
Freeze-proofing switch |
Kaobo (Shanghai) |
9 |
Pressure controller |
FENSHEN (Shanghai) |
10 |
Water pressure gauge |
CK (Taiwan) |
11 |
High-low pressure gage |
SK (Taiwan) |
12 |
AC contactor |
Schneider (France) |
13 |
Thermorelay |
Schneider (France) |
14 |
Temperature control |
Microcomputer LCD (AT, ST) |
15 |
Structure |
Unitary box type |
16 |
Surface treatment |
Sraying plastics |
17 |
Tank type |
Stainless steel heat preservation |
18 |
Outlet water temperature |
-2℃ |
19 |
Regrigerating fluid |
R22 |
20 |
Protector |
Compressor overload protection/ high-low pressure protection/ water break, shortage protection/ phase sequence protection/ pump overload protection/ air fan overload protection |
21 |
Regrigerating medium |
25% ethylene gycol solution |
6) Beverage mixing machine
Description:
IN-QHS-3000 Soda mixer is an automatic equipment specially designed for the production of various carbonated beverages such as lemon, cola and juice. Compared with domestically produced products of the same type, it has the characteristics of complete functions, accurate mixing, convenient and easy to adjust, and meets sanitary requirements. The structure is novel and reasonable, the structure adopts closed system, and can meet the requirements of cleaning and disinfection. Produces carbonated beverages and can easily adjust production capacity and water to the perfect syrup ratio. In addition, the combination of electrical control and other devices has the characteristics of high degree of automation, coordinated operation, continuous production, good mixing effect and large production capacity.
Working principle:
The WYH2000 automatic injecting gas-water mixer mainly consists of a vacuum section, a batching section and a gas-liquid mixing section.
- Vacuum section
The vacuum section consists of a closed circuit of the feed water inlet port by means of a solenoid valve, an air chamber, a vacuum pump and a vacuum tank equipped with a sprayer and a level controller.
- Matching section
The adjustment section consists of a ration pump, a slurry inlet line with a solenoid valve, and a syrup tank with a level controller. It consists of a syrup throttle valve and a venturi device. There are two adjustment handles with indicators on the venturi device. The size of the opening of the deaerated water and the sugar liquid outlet is shown, respectively. A certain amount of opening also reflects a certain ratio. For the amount of sugar required for a particular beverage, you can change the size of the opening by turning the sugar adjustment handle.
- Gas-liquid mixing section
The gas-liquid mixing section consists of a mixing pump, a CO2 inlet line with a pressure regulating device, a gas-liquid mixed venturi device, a soda storage tank with a level controller, and a soda water output line with a safety valve.
Technical parameters:
Model: |
IN-QHS-2000 |
Capacity: |
2000 L/H |
Mixing ratio(water:sugar): |
3:1—6:1 |
Mixing precision: |
≤2% |
Content of the CO2: |
≥4.0 times |
CO2 supplying pressure: |
1-1.3 MPa |
Heat exchanging area: |
3 m² |
CO2 consumption: |
3 m³/h |
CO2 purity: |
≥99.9% |
Compressed air consumption: |
6.5 m³/h |
Compressed air supply pressure: |
0.6-1 MPa |
Refrigerant: |
Ethylene glycol solution |
Refrigerant temperature: |
-2 ℃ |
Mixing temperature: |
25 ℃ |
Pressure at purified water inlet: |
0.3-0.4 MPa |
Pressure at syrup inlet: |
0.3-0.4 MPa |
Temperature at syrup inlet: |
≤25 ℃ |
Temperature at beverage outlet: |
1-2 ℃ |
Pressure at beverage outlet: |
≤0.65 Mpa |
Power: |
15 kW |
Dimension: |
3700*2200*2600 mm |
Weight: |
1850 Kg |
7) Hygienic pump
Technical parameters:
Model: |
YA10T/24 |
Capacity: |
5000Liter/hour |
Head: |
24m |
Power: |
2.2kw |
8) Plate type heat exchanger
Technical parameters:
Model: |
PH10M2 |
Function: |
used to low the sugar temperature |
Heating exchange area: |
10m2 |
Material: |
SS316L |
Mouth diameter: |
51mm |
Water cooling temperature: |
below 10 celsius degree |
9) Electric type CIP cleaning system
Description:
The whole system consists of water tank, alkali solution tank, acid solution tank, pump, plate heat exchanger
The CIP cleaning system is responsible for the cleaning of the filling machine.
The CIP cleaning system’s all cleaning process parameters (cleaning time, acid-base concentration, cleaning solution temperature, cleaning method) can be set on the operating touch screen.
When cleaning is required, specify the required cleaning equipment on the touch screen, select the cleaning method (three-step cleaning or five-step cleaning), and start the system, then the CIP equipment will complete the cleaning process according to the preset program.
Technical parameters:
Model: | CIP3X500L | |
Alkali tank volume: | 500 L | |
Acid tank volume: | 500 L | |
Hot water tank volume: | 500 L | |
Material of tanks: | SUS 304 | |
Wall-thickness: | 3 mm | |
Sanitary pump: | Water flow: | 3 m³ |
Pump head: | 25 m | |
Power: | 0.75 kW | |
Plate heat exchanger: | Model: BP2-JB-4 | |
Flow: 2000 L/H | ||
Temperature change: 30°C → 85°C | ||
SUS304 Stainless steel structure | ||
EPDM sanitary pad, SUS316 plate | ||
Alkali liquid pump: | 50 L/H | |
Acid liquid pump: | 50 L/H | |
Pipe fittings: | SUS 304 |
Filling & Post-Packaging Machine
1) Depalletizing machine
Features:
- Low position loaded pallet conveying system, and two pallets can be pre-stored. Carbon steel structure, carbon steel plate thickness 3.0 mm.
- Main depalletizing section, loaded pallets are depalletized layer by layer. Frame stainless steel structure, the inner guiding boards of three sides is 1.5mm thick SUS plate.
- High position platform with net conveying system, 4.0 meters high, 1.2 meters wide, 3 meters long, stainless steel structure, low friction plastic steel mesh chain.
- Low position conveying system for empty pallet discharging. Carbon steel structure.
- Loaded pallet lifting system, carbon steel structure.
- Electric-driven bottle pushing mechanism, carbon steel structure.
- Separating card-board placement platform. Stainless steel construction.
- High position operating platform and ladder. Carbon steel structure.
- The electric cabinet and the trunking for the cable wires are made of stainless steel.
- The machine uses electric-driven control method, and the lifting process is checked by the electric eye and automatically controlled, automatically positioning. The empty bottle is monitored by the electric eye and pushing onto the high-position conveyor
- Dimensions: 8500*2200*3200mm
Technical parameters:
Model: |
IN-XD-6000 |
Capacity: |
6000 B/H |
Main material of the machine: |
Carbon steel, stainless steel |
Main lifting motor: |
1.5 kW |
Bottle pushing motor: |
0.37 kW |
Loaded pallet feeding motor: |
0.75 kW |
Bottle conveying motor: |
0.75 kW |
Air consumption: |
500 NL/min |
Workshop minimum height: |
6000 mm (recommend install the machine at a low position with around -2000mm of the production line’s running height) |
Manufacturer: |
INPAKT |
2) Filling-sealing Duo-block
Description:
This machine is the filling and sealing technology imported from Switzerland. After digestion and absorption, the design and manufacture of the filling and sealing equipment can be widely used in the filling and sealing of gas drinks, beer and other cans. It is widely used for sealing aluminum cans, tin cans and PET cans. The equipment has stable performance, advanced technology, beautiful shape and complete functions.
BGF can filling and sealing machine is for carbonated beverage industries, it have such features as rapid filling and sealing speed, consistent height from the liquid level in the can to the can mouth after filling, stable machine operation, good sealing quality, beautiful and decent appearance, convenient use and maintenance, touch screen operation, frequency conversion speed adjustment, etc.
Features:
- Welded by SUS304. Product contact is SUS304 food grade;(SUS316 for option)
- High-efficiency rinsing-nozzles can spray water to any part inside the bottle;
- Corrosion-resistant bearings from NSK or SKF;
- Mechanical valve filling, flow meter filling, weighing filling or laser positioning filling for choice;
- Open design for gear transmission;
- Equipped with VFD control, more energy-saving;
- PLC control system is equipped;
- All electric components are supplied by the world-famous companies;
Technical parameters:
Model: | IN-GD-18-6 |
Capacity: | 6000 B/H (330ml) |
Can height: | 120-310 mm |
Can diameter: | 55-66 mm |
Can height: | 70-165 mm |
Filling pressure: | 0.25-0.35Mpa |
Filling heads: | 18 heads |
Filling method: | Isobaric filling |
Filling temperature: | 0-4°C |
Sealing heads: | 6 heads |
CO2 consumption: | 8 Nm3 / h |
Compressed air consumption: | 0.5Nm3/ h (0.4~0.5MPa) |
Installed power: | 3 kW |
Dimension: | 2400*2200*2200mm |
Height of conveyor: | 1200 mm |
Weight: | 3800 Kg |
Component list:
Items | Supplier, Origin |
PLC | Siemens, Germany |
Touch screen | |
Contactor | Schneider, France |
Thermal relay | |
Switches | |
Photoelectric electric sensor | Omron, Japan |
Pneumatic components | SMC, Japan |
Bearing | SKF, Sweden |
Detailed description
a) Filling Part:
Description:
Counter pressure filling.
The filling valve adopts constant pressure mechanical valve, which can fill quickly and sensitively with high liquid level accuracy.
Complete CIP cleaning function.
The filling valve orifice guide device and cylinder lift device are combined to ensure the accurate sealing of the bottle and filling valve and reduce the leakage of material from the tank orifice.
Depending on the height of tank type, manual lifting can be achieved to meet the filling requirements.
The machine has a gear transmission with high efficiency, low noise, long life, convenient maintenance and sufficient lubrication. The main motor speed of the machine is controlled by frequency converter.
The bottle guiding system is simple in structure and can be changed quickly and conveniently according to the tank type.
The whole machine is controlled by PLC automatically, and the fault is displayed online, such as bottle plugging and lid missing.
It has the safety protection function of no open valve without tank, no cover and stop with no cover.
The material in the filling cylinder is automatically controlled, and the liquid level height is detected by the level sensor to ensure the stable liquid level and reliable filling.
Key parts and electrical components of the machine are imported.
b) Capping Part
Description:
The sealing part seals the lid on the cans of the filled product and is sent by the conveyor chain to the latter process.
The sealing roller is made of high hardness alloy (HRC>62), and the sealing curve is precision machined by optical curve grinding to ensure the sealing quality and normal operation of the machine.
The machine has a tank under cover, no tank under cover control system, to ensure the normal operation of the machine, reduce cover loss rate.
Manually put the aluminum cover in the chute by the cover gravity and the thruster for the lower cover.
According to the tank type of different height, the capping machine can be manually lifted to meet the requirements.
3) Nitrogen dosing system (not included in the price list)
Features:
- Pulse injection modes can reduce pressure and the cost of liquid nitrogen, decrease operating costs.
- Vacuum insulation – Low rate of evaporation (NER) 0.15L/H, liquid nitrogen machine can decrease operating costs.
- Nozzle Blanketing can prevent outside air into spray chamber internal frost.
- Liquid nitrogen level positioning control, Horizontal pressure stable, can improve the liquid nitrogen dose accuracy, and at the same time reduce liquid nitrogen flash loss.
- Liquid level by dynamic positioning control system, there will be no problem of the electronic level control system and electrically operated valve.
- Liquid gas separator, to ensure the super cold of the liquid nitrogen, improve the quality of pure liquid, help to liquid nitrogen dose accurately.
- Buffer nitrogen filled function, effectively prevent the liquid nitrogen rebound spill, liquid nitrogen pick up quantity is stable, also ensure that the tank pressure stable. Equipped with a filter 10um, to remove particle pollution.
4) Can Pasteurizing Machine
Description:
The heat tunnel is used to warm bottles up to room temperature, for preserving taste and ensuring the quality of the shrink wrapping/packing processes. The machine sprays high temperature water onto the bottle to warm the bottles up. The cooling area is divided into five section, the temperature gradually increases while bottles pass by sections. When coming out of the tunnel, the bottles reach the room temperature.
Features:
- Highly reliable conveyor, flexible and convenient shifting system.
- The conveyor belt for conveying bottles is a high-strength plastic chain net with good strength and certain wear resistance.
- The main drive adopts a continuously variable motor, which can easily change the conveying speed of the conveyor belt.
- Efficient water spraying system.
- The machine adopts neatly and orderly arrangement of atomizing nozzles on the top of the chain plate to spray water to warm the parts of the bottles evenly, so that the spray water can be fully utilized and the spraying coverage area is large.
- Temperature control is sensitive and easy to set.
- This machine adopts temperature control system, high temperature control precision and sensitive response.
Technical parameters:
Model: |
WPJ-6-10 |
Capacity: |
6000 C/H (330ml) |
Material: |
SUS304 |
Motor power: |
0.75 kW |
Dimension: |
6000*3000*1550 mm |
Weight: |
6600 Kg |
Steam consumption: |
200 Kg/H |
Air pressure: |
0.7 Mpa |
5) Blow dryer
Description:
- The blower adopts a fan as the air source.
- An air knife type structure, and the size of the sealing can be adjusted.
- The top side and the two vertical sides of bottles can be blown to dry thoroughly.
- Easy for labeling, printing, packing operations.
Technical parameters:
Model: |
IN-CGJ |
Capacity: |
20000 B/H |
Length: |
800 mm |
Dimension of the blower: |
40*40 mm |
Power: |
7.5 kW * 2 |
Material: |
Stainless steel 304 |
Dimension: |
1200*350*1400 mm |
6) Vacuum leakage checker
Description:
The internal pressure of the cans filling is monitored in real time, It can quickly detect and reject, reject cans. Users can monitor whether the front-end equipment is running normally and prevent the unqualified products from being adversely affected by the market. If necessary, the operator can set the function of automatically stopping the front-end equipment to reduce the loss.
Features:
- The detection system adopts Siemens PLC.
- High-precision dynamic tracking sensor, can detect minute pressure change data.
- Give timely judgment results through PLC calculation and comparison.
- Real-time monitoring of each tested product passed.
Technical parameters:
Model: |
NYJ-200 |
Detection head: |
1 |
Production capacity: |
0~150 cans/min |
Using range: |
Can diameter: φ52.5~φ99mm |
Can height: H65~H166mm |
|
Power: |
150W |
Dimension: |
530*150*350mm |
Weight: |
40 Kg |
Dimension: |
780*350*800mm |
7) Liquid level checker
Description:
ZJZ200 filling liquid level detector is a liquid level detecting instrument developed by our company to reach the advanced level at home and abroad. After the low-energy photon source interacts with the measured substance, the ray intensity changes according to the position of the detected material surface to control the volume of the filled liquid material. Due to its non-contact measurement method, the problem that the conventional weighing method cannot measure the volume of liquid material in the production line can be solved fundamentally.
Technical parameters:
Model: |
ZJZ200 |
Production capacity: |
0~180 cans/min |
Using range: |
Can diameter: φ52.5~φ99mm |
Can height: H65~H166mm |
|
Power: |
150W |
Dimension: |
530*150*350mm |
8) Automatic PE film shrink wrapping machine
Features:
- Frequency control, secondary bottle transport device.
- The whole set which are push bottle, heat sealing cutting adopt pneumatic structure.
- Inductive switch control film length.
- Touch screen, PLC control system advanced reliability of the equipment function.
- Circular wind machine, reassure well-proportioned temperature of the shrink furnace.
- Strong cooling system can reassure finalize the design quickly.
- Heat-fast Teflon transport net, transport steady, high strength and stand wear and tear.
- Frequency conversion timing net transportation structure.
- The height of the conveyor belt can be made according to the user, adjustable range±50mm
- Bottle transport machine can satisfy the direction of the user, it can prolong and shorten
- Pterygoid stainless iron heating system, durability.
- Satisfy the bear storage rack device of the short duration for the product, assure consecutive work for the production line.
Technical parameters:
Model: |
IN-MB-50A |
Material of shrink film: |
PE, PVC |
Thickness of the film: |
0.03-0.15 mm |
Max packing size: |
600*400*350 mm |
Temperature of the heating tunnel: |
160-260 °C |
Thickness: |
0.035mm |
Capacity: |
10-12 package / min |
Automatic dividing formation: |
4*3, 3*2 |
Power |
20 kW |
Actual consumption: |
15 kW |
Dimension: |
5050*3300*2100 mm |
Weight: |
1.2 ton |
9) Belt conveyor & Buffering system
Description:
The operation efficiency of the production line is mostly up to the configuration of the conveyor line. The configuration must take into account the short-term shutdown of the rear-end equipment (for example, replacement of labels, etc.), ensuring the shutdown doesn’t affect the operation of the front-end equipment, and should be able to connect the front equipment and rear equipment well to make the whole the production line achieve high operation efficiency.
Our production line’s layout fully considers the relationship between customer investment and production line efficiency. Based on the world’s advanced technology, the above requirements can be well achieved. The mechanical structure is a new design, most of the components are formed by stamping or bending, which has the advantages of good rigidity, light weight and good interchangeability. The transmission method features reliable operation and convenient maintenance, which is suitable for conveying bottles with diameters of Ø40-Ø110mm. The electric control system adopts PLC (On the Rinsing-filling-capping tri-block) to control the operation of the whole container conveying buffer system, and automatically conduct the functions of running speed acceleration and deceleration and automatic buffering.
Features:
- The bottle belt is synchronously tracked with the host or the upstream and downstream equipment, which are connected to control system.
- The bottle does not fall, does not jam, and does not block during the conveying process.
- According to the user’s needs, the buffer platform can be set in front of the labeling machine (the buffering time is usually about 1-2 minutes).
- When replenish PE label, the filling process proceeds, the filled bottles are stored on the buffer platform. After finishing replenishing PE label, the labeler starts labeling, the line gets back to synchronizing production.
- After replenishing, the labeling machine produces at a higher speed to fill the platform with labeled bottles again, and then resumes the synchronous production speed.
- The conveyor belt structure is modular design, the parts are interchangeable, compact, low noise, easy to install and maintain, and can be combined according to different capabilities and bottle types, which has great flexibility.
- Electric control design is advanced and reasonable, and the control method can be designed according to the customer’s requirements, and the required electrical control components can be selected to further improve the smoothness of transportation.
- The control switch position is reasonably set according to the layout of the conveying system or the customer’s demand, which is convenient for the user to operate.
Technical parameters:
Motor power: |
0.37 kW / 6m |
Width of the conveyor: |
110 mm |
Height: |
1050 mm |
Thickness of the steel plate: |
2 mm (SUS304) |
Bottle volume: |
200-3000 ml |
Bottle Diameter: |
50-100 mm |